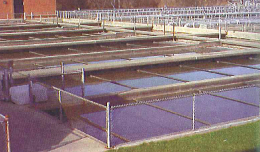
Peel Lakeview Atıksu Arıtma Tesisi![]()
ÖZET Mississauga, Ontario’da bulunan Lakeview Atıksu Arıtma Tesisi (AAT), Peel Bölge İdaresinin bünyesindedir ve Ontario Clean Water Agency (OCWA- Ontario Temiz Su Ajansı) tarafından işletilmektedir. Bu tesisin çamurları yaklaşık 30 yıldır akışkan yataklı yakma sistemlerine (FBI) haiz yakma fırınlarında berteraf edilmektedir. Tesis, Ontario Gölü’nün kıyısında, Toronto metropolünün hemen batısında yer almakta ve Mississauga, Brampton ve Caledon şehirlerine hizmet etmektedir. Yıllık ortalama debisi 118 mgd (450.000 m3/gün)’dir. Son birkaç on yıldır tesiste üretilen ve Clarkson Atıksu Artıma Tesisinden (Peel bölgesinde, Mississauga’nın batısında yer alan ikinci AAT) gelen çamurlar Zimmerman Prosesi ile (Zimpro) ısıl işleme tabii tutulup, yüzde 38 katı maddeye kadar susuzlaştırılıp, 3 adet soğuk hava girişli (CWB) akışkan yataklı fırında yakılmaktadır. Zimpro prosesinin sebep olduğu yüksek bakım maliyeti ve kötü koku nedeniyle, Peel Bölge İdaresi ısıl işlemli prosesi iptal ederek, mevcut üç adet soğuk hava girişli (CWB) akışkan yataklı yakma fırını yerine dört adet, 110 US ton/gün kuru çamur kapasiteli, sıcak hava girişli (HWB) akışkan yataklı yakma fırını tesis etme kararı aldılar. Bugün itibariyle herhangi bir işleme tâbi tutulmamış Lakeview tesisinin çamuru, santrifüjlü dekantörler kullanılarak yüzde 27 kuru madde olacak şekilde susuzlaştırılmakta ve sıcak hava girişli akışkan yataklı fırınlarda otomatik olarak yakılmaktadır. İşleme tabi tutulmamış çamurun karışım oranı 60/40 oranında primer ve aktif biyolojik çamurdan oluşmaktadır. Çamur, orijinal olarak evsel kaynaklı olup, yüzde 30’u endüstriyel tesislerden çıkan çamurdur. İlk iki CWB akışkan yatak 1982 yılında, üçüncü CWB sistemi ise 1994 yılında devreye alınmıştır. Bu üç sistem de atık enerji kazanlarını ve ventüri gaz yıkayıcısını da ihtiva eden doldurma-boşaltma (push-pull) sistemiyle çalışıyordu. Tesiste üretilen buhar, Zimpro ısıl işleminde kullanılmaktaydı. Şubat 2006 tarihinde sıcak hava girişli HWB dört fırından ilki monte edilip işletmeye alındı. Yeni sistemde gövde-borulu ısı eşanjörü kullanılarak yakma havası 1230 °F’a kadar (665,5 °C) ön ıstmaya tabi tutulmakta ve bu sayede ilave yakıt kullanımı büyük oranda azaltılmaktadır. Çoklu ventüri tipi gaz yıkayıcısı aracılığıyla çıkan gazlar arıtılmakta ve hava kirliliği önlenmektedir. Sıcak hava girişli HWB yeni fırın, işletmeye alındığı Şubat 2006’dan itibaren 7 gün, 24 saat kesintisiz çalışmakta olup, çok az ilave yakıta ihtiyaç duymakta ve kum ilavesi gerekmemektedir. İlk performans testleri sonucunda tesisin, yürürlükteki emisyon yönetmeliğindeki sınır değerlerini fazlasıyla karşıladığı görülmüştür. Zimpro sisteminin değiştirilmesiyle ilgili geçiş döneminin bütün detayları ve işleme tabi tutularak yakılan çamurla herhangi bir işlem görmeden yakılan çamur arasındaki teknik ve ekonomik farklılıklar aşağıda detaylarıyla açıklanmaktadır. 2009 yılına kadar akışkan yataklı dört adet fırının da devreye girmesiyle Lakeview Tesisi dünyanın en büyük çamur yakma tesisi oldu. Peel Bölge İdaresi, HWB tipi akışkan yataklı çamur yakma fırınlarını kullanarak, bu tip tesislerin İdareyi, ruhsat veren kontrol teşkilatlarını ve halkı memnun eden, ekonomik ve çevre dostu çamur berteraf sistemleri olduğunu göstermiştir. GEÇMİŞ The Lakeview Atıksu Arıtma Tesisi Mississauga, Ontario’da yer alır ve Mississauga, Brampton ve Caledon şehrinde yaşayan bir milyondan fazla kişiye hizmet eder. Tesisin yıllık ortalama tasarım kapasitesi 118 mg/gün (446.000 m3/gün)’dür. Lakeview tesisinin prosesi giriş yapısı, kum ve yağ giderme, primer arıtma, sekonder arıtma ve dezenfeksiyon kademelerinden oluşmaktadır. Giriş yapısı 6 mm aralıklı, perfore saçlı elevatör tipi mekanik ızgaralardan oluşmaktadır. Bu aşamada tutulan elek üstü malzemeler atık konteynerlerine atılmadan önce temizlenip susuzlaştırılmaktadır. Eleklerden geçen atıksu, içindeki kumdan temizlenmesi amacıyla, vorteks kum hücresine ve kum yıkayıcılarına gider. Suyu alınan kum, atık konteynerlerinde depolanır. Primer arıtma, primer durultucular ve köpük toplayıcılardan oluşur. Çökelen maddeler ve tanklardan gelen köpükler, katı madde işleme tesisinde bulunan karıştırma tanklarına gönderilir. Primer tanklardan çıkan atıksu, sekonder arıtma tanklarına gönderilir. Sekonder arıtma, havalandırma tankları ve sekonder durultuculardan oluşur. Aktif çamur tanklarında üretilen atıksu çamuru (WAS) kısmen havalandırma tanklarına geri gönderilir. Kalan çamur katı atık işleme tesisindeki WAS tanklarına pompalanır. Sekonder çökeltme tanklarından çıkan su, kimyasal işleme tabi tutularak Ontario Gölü’ne deşarj edilir. Katı atık işleme binasında, WAS tanklarından gelen WAS çamuru santrifüjlü dekantörler aracılığıyla yaklaşık yüzde 3-5 kuru maddeye yoğunlaştırılır. Daha sonra bu çamur, karıştırma tanklarında primer çamurla yüzde 40, yüzde 60 oranlarında (WAS’dan Primer’e) karıştırılır. 1980’den beri, tesiste üretilen karıştırılmış çamur ve Clarkson Atıksu Arıtma Tesisinden gelen çürütülmüş çamur, Zimpro prosesiyle işleme tabi tutularak, vakum filtresi aracılığıyla yüzde 38- 50 KM’ye susuzlaştırılmış ve iki adet CWB akışkan yataklı termik oksidasyon (TOX1 ve TOX2) fırınlarında yakılmıştır. Her bir fırının günlük kapasitesi 88 ton (kuru madde)’dur. Lakeview tesisinde yakılan çamurun üçte biri Clarkson AAT’nden gelmektedir. Clarkson 43 mgd (162500 m3/gün) kapasiteli bir tesis olup, Lakeview’den yaklaşık 15 km uzakta, Batı Mississauga’da yer almaktadır. Revizyondan önce (2005’den önce) Clarkson tesisinin çamuru sıvı formda Lakeview tesisine günde 30 kamyonla taşınmaktaydı. 1994 yılında, Lakeview tesisinde, ilave Zimpro sistemini de ihtiva eden 110 ton/gün kuru madde kapasiteli üçüncü bir CWB termik oksidasyon (TOX3) fırını daha devreye alındı. Her üç fırının çıkışında atık ısı kazanları vardı. Bu atık ısı kazanlarından elde edilen buharın bir kısmı Zimpro işlemi için kullanılırken, kalan enerji, binaların ıstılması amacıyla kullanılmaktaydı. 2002 yılında karıştırılmış çamurun kuruluğunu yüzde 27’ye çıkaran iki adet santrifüjlü dekantör tesis edildi. Fizibilite çalışması Lakeview tesisinin kapasitesinin yetersiz olmaya başlaması, Zimpro çamurunun neden olduğu yoğun kötü koku ve ileride tesislerin kapasitelerinin artırımlarının gündeme geleceği gerekçeleriye 2002 yılında Peel Bölge İdaresi, hem Lakeview hem de Clarkson tesislerinden çıkan çamurun berterafı ile ilgili muhtelif alternatifleri değerlendirecek bir çalışma başlattı. KMK Müşavirlik Limited ve Black and Veatch konsorsiyumu, 2031 yılına kadar olan dönemi kapsayacak biyokatı yönetim planını oluşturmaları için seçildi. Biyokatı master planı Peel bölgesinden çıkan çamurun nakliyesi ve bertarafı için bütün alternatifleri değerlendirecek bir plan olacaktı. Bu çalışmada 2031 yılı için dikkate alınan çamur miktarları Lakeview için 165 US ton kuru madde ve Clarkson için 89 US ton kuru maddeydi. Çamurun muhtelif berteraf alternatiflerini değerlendiren Master Plan 2003 yılında bitirilerek teslim edildi. Bu rapor, muhtelif alternatiflerin çevreye olan etkisini, esnekliğini, geri dönüşüm imkanlarını, işletme ve yatırım maliyetlerini bugünkü net değere çevirerek detaylı olarak incelemekteydi. Bu raporda üç alternatif olurlu (feasible) bulunarak değerlendirildi: “Akışkan yataklı fırında yakma”, “Çıkan granüllerin gübre olarak kullanılacağı termik kurutma”, “Susuzlaştırılıp araziye serme”. Bu üç alternatif kullanılarak Clarkson ve Lakeview tesislerinin her ikisinin teknolojik konfigürasyonlarını kapsayan 11 ayrı yönetim alternatifi belirlendi. En önemli yedi alternatif, ABD Doları cinsinden, bugünkü net yatırım maliyetini ve beher kuru US tonu için işletme maliyetini içerecek şekilde Şekil 1’de grafik olarak verilmiştir Çamurun kurutularak araziye serilmesi veya çamurun susuzlaştırılarak araziye serilmesi alternatifleri, nakliye maliyetleri, koku problemi, Peel bölgesi ve komşu bölgelerdeki tarımsal arazilerin yeterli büyüklükte olmamasından ve çiftçilerin bu çamurlara yeterli ilgiyi duyup duymayacaklarının kesin olarak bilinememesinden dolayı elimine edildi. Bu sebeplerden dolayı bu çalışma, Lakeview tesisindeki çamurun bertarafı için akışkan yataklı yakma fırınlarının kullanılmasına devam edilmesinin olabilecek en iyi çözüm olacağını belirledi. Tesisin yakınında ve bölgedeki kamyon trafiğini azaltmak amacıyla Clarkson tesisinden, yakılması için Lakeview’e getirilecek çamurun susuzlaştırılarak taşınmasına karar verildi. Tablo 1’de susuzlaştırılarak Lakeview’e taşınan Clarkson çamurunun nakliyesinde yüzde 88’lere varan bir azalmanın olduğu görülmektedir. Atık ısı geri kazanımı da dikkatli bir şekilde değerlendirildi. Yanma havasını ön ıstmaya tabii tutacak gövde borulu ısı eşanjörünü, kurutma ve bina ısıtılmasında kullanılacak veya akışkanlığı sağlayan hava blowerini çevirecek türbinin ihtiyaç duyduğu buharı üretecek atık ısı kazanını da ihtiva eden değişik atık ısı geri kazanım alternatifleri değerlendirildi. Çok komplike oluşu, işletme ve yatırım maliyetlerinin yüksek oluşu nedeniyle Bölge İdaresi, buhar üretim sisteminin iptal edilmesine ve en verimli berteraf yöntemi olarak hava ön ısıtmalı, sıcak hava girişli yakma fırınının kullanılmasına karar verdi. Isı geri kazanım sistemi, yakma havasını 665 °C’ye ısıtan gövde borulu bir eşanjörden oluşmaktadır. Bu sıcaklık, akışkan yataklı HWB fırında, santrifüjlü dekantörle yüzde 27 KM’ye susuzlaştırılan çamuru otomatik ve sürekli olarak yakmaya yetecek bir sıcaklıktır. Bölge İdaresi ayrıca mevcut soğuk hava girişli fırınların rehabilite edilerek sıcak hava girişli fırınlara dönüştürülmesi alternatiflerini de değerlendirmiştir. Sonunda en iyi çözüm olarak son teknoloji ürünü yeni HWB fırınların kullanılmasına karar verilmiştir. YAKMA SİSTEMİNİN TANIMI Zimpro Çamurunun Bertarafında Kullanılan Soğuk Hava Girişli Sistem Zimpro çamurunun bertarafı için kullanılan CWB sisteminin akış şeması Şekil 2’de verilmektedir. Öncelikle ısıl işleme tabi tutulmuş çamur, çökeltme tankında susuzlaştırılır. Sonra, tankın tabanından alınan yüzde 15 KM’li çamur, vakum filtreleri kullanılarak yüzde 38 KM’ye çıkarılır ve üç adet CWB fırına pompalanır. CWB fırın metal plakalı hava dağıtım sistemi ve çelikten mamül (Refraktör tuğlayla kaplanmamış) hava giriş odasıyla techiz edilmiştir. Bu yüzden ilk çalıştırmada kullanılan iki adet ön ısıtma brülörünün yanma odasına monte edilmesi gerekmiştir. Yanma odası silindirik yapıda olup, hava girişi yatak üzerinden yapılmaktadır. CWB’ye çamurun girişi iki adet besleme girişinden yapılmaktadır. Sistem yükleme-çekme (push pull) tip olup, akışkanlık havası blowerla verilip, çıkan gaz cebri çekme fanıyla alınır. Çıkış hattında Zimpro prosesinin ihtiyacı olan 450 psig basıncındaki sature buharı temin eden atık ısı kazanı, ekonomizer, kazan besleme suyu pompaları ve kışın ihtiyaç duyulan bina ısıtma sistemleri vardır. Çıkan gazlar venturi tipi ve tavalı gaz yıkayıcısı ile temizlenir. Atık ısı kazanından ve venturi gaz yıkayıcısından çıkan sıvı çamur formundaki küller, dışarıda bulunan lagünlere depolanma ve susuzlaştırılmak amacıyla pompalanır. İşleme Tabi Tutulmamış Çamurun Bertarafını Sağlayan Sıcak Hava Girişli Sistem HWB sisteminin proses diyagramı Şekil 3’te gösterilmektedir. Yoğunlaştırıcıdan alınan ve yüzde 3 ila yüzde 5’lik KM’ye sahip çamur, iki adet (toplamda 6 adet) santrifüjlü dekantör aracılığıyla yüzde 27 KM’ye susuzlaştırılır ve piston pompalar aracılığıyla 4 adet besleme girişinden yakma fırınının içine pompalanır. Akışkan yataklı kazanın girişinde refraktör tuğlayla kaplı kubbe formunda bir dağıtıcı ile yine refraktör tuğlayla kaplanmış bir rüzgar odası vardır. HWB sisteminde ilk çalıştırma için gereken enerji, bu giriş odasına yerleştirelen brülörler aracılığıyla çok daha hızlı ve verimli bir şekilde temin edilir. Burada gerektiğinde kullanılmak üzere fuel oil ve doğalgazla çalışan ilave yakıt sistemleri de bulunmaktadır. Yanma Odası yaklaşık 843 °C (1550 °F) tasarım sıcaklığında çalışmaktadır. Reaktörün yapısı yukarı doğru genişleyen biçimdedir. Bu sayede hava hızı düşürülerek kumun ve ağır partiküllerin kaçışı engellenmiş, karbonun yanma süresi artırılmıştır. İlave yakıt tüketimini minimize etmek amacıyla giriş havası, fırından çıkan egzos gazlarını kullanarak gövde borulu bir eşanjörde yaklaşık 1230 °F (665,5 de °C)’a ısıtılmaktadır. Isı transferinin azaltılması ve hava giriş sıcaklığının düşürülmesi gerektiği durumlarda kullanılmak üzere gövde borulu eşanjörde hava by-pass sistemi bulunmaktadır. Hava kirliliğini önleme sistemi ıslatma sistemini, sıkıştırmalı bir gaz yıkayıcıyı ve çoklu sabit ventüri gaz yıkayıcıyı ihtiva eder. Yıkama işlemi çıkış gazının sıcaklığını düşürür ve ayrıca gaz içerisindeki külü ve partikülleri sıvı çamur haline getirir. Sıkıştırmalı ve çoklu ventüri tipindeki gaz yıkayıcıları hem gaz sıcaklığını düşürür, hem de gaz içinde kalan külleri ve partikülleri tutar. Yıkama kademesinden, sıkıştırmalı ve çoklu ventürüli gaz yıkayıcılarından gelen çamurlar, bir kül tankında toplanıp dışarıda buluna bir çökeltme lagününe pompalanır. MASTER PLAN Kısa ve uzun vadeli genişlemeyi temin edebilmek amacıyla Bölge İdaresi ve müşavir firmalar, mevcut üç adet CWB Zimpro Sistemini devre dışı bırakmaya ve yerlerine 110 kuru US ton kapasitesinde dört adet HWB fırını tesis etmeye karar verdiler. Zimpro sisteminin devre dışı bırakılmaya başlamasından, tamamen kapatılmasına kadar geçen süre çok dikkatli bir şekilde planlandı. 1. kademede 2 adet susuzlaştırma dekantörü devreye alındı ve TOX3 CWB fırını 60 US ton/gün kapasiteye ayarlandı. Bu sayede herhangi bir ilave Zimpro hattına gerek kalmadan tesis kapasitesi artırılmış oldu. 2. kademede Zimpro oranını yüzde 50 azaltan HWB sistemiyle mücehhez yeni bir TOX4 fırını tesis edildi. 3. kademede daha önceden tesis edilen iki santrifüjlü dekantörün ve kek pomplarının yerleri değiştirildi. Bu sayede Zimpro hattının kapasitesi yüzde 25 daha azaltılmış oldu. 4. kademede Clarkson’dan çamurun susuzlaştırlmış olarak gelmesi sayesinde Zimpro sistemleri tamamen devre dışı kaldı. Master planın değişik safhaları Tablo 2’de gösterilmiştir. KADEMENİN GERÇEKLEŞTİRİLMESİ / TOX4’ün MONTAJI 1. Faz 2002 yılında, işleme tabi tutulmamış çamuru yüzde 27 kuruluğa kadar susuzlaştıracak santrifüjlü dekantörlerin montajıyla başlamış olsa da, 2. Faz yeni HWB TOX4 fırınlarının montajı ve bu fırınların içine yerleştirileceği yeni binanın yapımı aşamasıdır. 2. Faz, 3 Aralık 2003 tarihinde Degremont Technologies Infilco’nun Yakma Sistemi sağlayıcısı olarak seçilmesiyle başlamıştır. Sistem sağlayıcının temin kapsamı, ekipmanın mühendisliğini yapmak ve ekipmanı temin etmektir. Montaj ise akışkan yatağın ve refrakter tuğlanın montajıyla sınırlıdır. Sistem sağlayıcı ayrıca kalan bütün ekipmanların ilk çalıştırması, işletmeye alınması ve işveren personelinin eğitimi için süpervizyon hizmetleri vermekten de sorumludur. Tesisin modernizasyonunun çok hızlı ilerlemesinden dolayı Degremont Technologies Infilco’nun Genel Mütehhidin (GC) seçiminde ihtiyaç duyulacak projeleri hazırlayabilmesi için sadece 8 ayı vardı. Önceden yapılan zamanlamaya uygun olarak Kenaidan Contracting LTD şirketi Genel Müteahhit olarak Temmuz 2004 tarihinde seçildi. Kasım 2004’de şantiye kazı işleri tamamlanıp ekipmanların sevkiyatı başladı. Ekipmanların montajı Ekim 2005’de tamamlandı. Bina Ocak 2006’da bitirildi, işletmeye alma ve çalıştırma işlemleri Mart 2006’da başarıyla tamamlandı. 2. Faz TOX4’ün montajı, işletmeye alınması ve yeni binanın yapımı da dahil olmak üzere 2 yıl 3 aylık bir sürede tamamlandı. Faz 2 tesisin günlük işletilmesinde herhangi bir olumsuzluğa neden olmaması için çok dikkatlice planlandı. Faz 2’nin yapımı aşamasındaki önemli tarihler Tablo 3’te verilmiştir. Bu tarihler Peel Bölge İdaresi Yönetim Stratejik Planlamasındaki hedef tarihlerle uyumludur. Bu aşamanın başarısı takım çalışmasındaki mükemmelliyete ve Bölge İdaresi, Müşavir ve Genel Müteahhit ile yapılan başarılı koordinasyona bağlıdır. TOX4’ün ve yeni binanın resimleri Şekil 4 ve 5’te verilmiştir. TOX 4’ün PERFORMANS TESTLERİ Tesisin yönetmeliklere uygunluğunu gösteren baca testleri Mart 2006’da gerçekleştirildi. Testler, tesisin emisyonlarının, Ontario Çevre Bakanlığının toplam hidrokarbonlar, hidrojen klorit, dioksins ve furanlar, toplam askıdaki katı madde, ağır metaller: civa, arsenik, kadmiyum, krom, kurşun ve nikel emisyonlarıyla ilgili yönetmeliklerine uygun olup olmadığını tespit etmek amacıyla yapıldı. TOX4 perfomans şartlarını büyük bir farkla hem de ilk denemede başarıyla yerine getirdi (AMEC Toprak ve Çevre, 2006). Tesis, test süresince 9200 lb kuru madde/saat kapasitede (4168 Kg/saat) çalıştı. Çıkış gaz sıcaklığı ve fazla hava sürekli kontrol edildi. Kuru gaz cinsinden sıcaklığın 1500 °F (815,5 °C)’ın altına oksijenin de hacimsel olarak yüzde 6’nın altına düşmemesine özen gösterildi. Ventüri gaz yıkayıcısındaki basınç düşümü asgari 40 inç (1 metre) su sütunu olarak muhafaza edildi. Tablo 4’te kayıt edilen ortalama emisyonları, uygunluk durumunu ve her bir kalem için yüzde olarak emisyon limitleri görülüyor. Yanma gazlarının içerisindeki Azot Oksitler (NOx), Kükürt Dioksit (SO2) ve Karbon Monoksit (CO)’de Sürekli Emisyon Takip Sistemi (CEMS) ile önceden belirlenen takip süresi boyunca sürekli olarak örneklenip analiz edildi. Günde yapılan üç test sonucunda bu kirleticilerin ortalama emisyon değerleri sırasıyla kuru gaz olarak 39.0 ppmv, 53.9 ppmv ve 6.1 ppmv olarak belirlendi. İŞLETME GEÇMİŞİ - CWB ve HWB SİSTEMLERİ ARASINDAKİ ÖNEMLİ FARKLILIKLAR HWB TOX4 işletmeye alındığı Şubat 2006’dan itibaren problemlerinin ve inşaat işlerinin sebep olduğu kesintiler dışında sürekli olarak 7 gün 24 saat çalışmaktadır. Zimpro prosesinin iptal edilmesiyle tesite ortaya çıkan kötü kokuda ciddi bir azalma meydana gelmiştir. Tesis tasarım değerlerinde işlem görmemiş çamuru yakmakta, çok az ilave yakıta ihtiyaç duymakta ve işletmeye alındığından itibaren sıfır kum kaybıyla çalışmaktadır. Eski CWB istemi ile yeni HWB sistemi arasındaki önemli farklılıklar şunlardır: Isı Geri Kazanım Sistemi: Atık ısı kazanı ile karşılaştırıldığında gövde borulu ısı eşanjörü herhangi bir bakıma ihtiyaç duymamaktadır. İşletmesi çok daha kolaydır ve özel eğitimli operatöre ihtiyaç duymamaktadır. Besleme Sistemi: İşlem görmemiş yüzde 27 kuruluktaki çamuru pompalamak (Önceki sistemde işlem görmüş ve yüzde 38 kuruluktaki çamuru pompalamaya göre) çok daha kolaydır. Ayrıca çamurun dört değişik noktadan enjekte edilmesi, akışkan yatakta çok daha iyi bir yanma sağlamaktadır. Yerleştirilen 4 adet termokapıl aracılığıyla yatak sıcaklığı 2,7 °C hassasiyetle ölçülebilmektedir. CWB sisteminde hassasiyet 8,3 °C’dır. Ön Istma Brülörü: CWB sisteminde iki adet ön ısıtma brülörü, yanma odası duvarlarına monte edilmiştir. Alevlerin yönü kum yatağına doğrudur. CWB sistemiyle soğuk çalıştırmada brülör devreye belli aralıklarda girer, kum yatağı da aralıklarla yükseltilerek, işletme sıcaklığına ulaşılıncaya kadar bu yöntemle devam edilir. HWB sisteminde ise iki adet olan ön ısıtma brülörü 1 adede indirilerek fırının altında yer alan giriş hava bölmesine yerleştirilmiştir. Bu sayede hem soğuk, hem sıcak çalıştırmada, işletme sıcaklığına çok daha az yakıtla çok daha kısa sürede ulaşılmaktadır. CWB sisteminde, soğuk konumdan işletme sıcaklığna ulaşma süresi tipik olarak 30 saat civarındadır. Bu süre HWB sisteminde 16 saattir. Tipik bir sıcak başlama süresi ise CWB için bir saattir. HWB için gereken süre bu sürenin yarısıdır. Bu sürelerdeki kısalığın sebebi, brülörün hava giriş odasına alınmış olması ve ısı eşanjörüdür. Kum Kaybı: CWB tipi fırınlarda sürekli kum takviyesine ihtiyaç duyuluyordu. Kum, silika bazlı olmayan beyaz şimşek kumuydu. CWB sisteminde akışkan yatakta ortaya çıkan kum kaybını telafi etmek için saatte yaklaşık 50 Lb kum ilave etmek gerekiyordu. HWB sisteminde ise yeşil olivine kumu kullanılıyor. Her ne kadar bu kum üç kat daha pahalı olsa da pratik olarak işletmeye alındığı tarihten itibaren hiç ilave etme gereksinimi duyulmadı. Olivine kumu aşınmaya olan dayanıklılığıyla bilinmektedir. Ayrıca HWB sisteminin yanma odası yukarı doğru genişleyen gözyaşı damlası şeklinde tasarlanmış olduğu için gaz hızında 3 ft/sn’den 2.1 ft/sn’likbir hıza yavaş bir düşüş temin eder (aşağıdan yukarı doğru). CWB sisteminde yanma odası düz silindirik şekildedir. Gaz hızı yaklaşık 2,5 ft/sn’dir. Olivine kumunun dayanıklılığının ve yanma odasının şeklinin kum kaybını engellediği düşünülmektedir. Yatak-Üst Havası: TOX4’de yatak üst havası kullanılmamaktadır. Bu açıdan çok daha basit ve düşük maliyetlidir. CWB’de görülen kum kaybının önemli bir sebebi bu üst hava kullanımı olabilir. Sadece Doldurma yerine Doldurma-Boşaltma: Yeni tesis edilen HWB sistemi sadece doldurma tipi olup, burada akışkan yatak için gereken hava blowerla verilir. CWB sisteminde akışkan yatak havasını basan blower ile içerideki havayı çeken çebri çekme fanı (push-pull) sistemi vardır. Sadece doldurmalı sistemin işletilmesi ve maliyeti doldurma-boşaltma sistemine göre daha düşüktür. Azot Oksit Emisyonu: Tablo 6’da verildiği şekilde HWB sisteminden deşarj edilen Azot okistlerin miktarı 39.6 ppmv’dir. CWB sisteminde ise bu değer 1989 yılında (Van De Kraats et al, 1991).ppmv tarafından ölçüldüğü şekilde 491 ppmv’dir. HWB’deki Nox emisyonlarının düşük olmasının TOX4’ün bugün yaktığı çamurdaki katı madde oranlarının Zimpro prosesindeki yüzde 45-50’lik KM oranlarına nazaran daha düşük (yüzde 27 KM) olması yüzünden olduğu düşünülmektedir. Bu gerçek Dangtran (Dangtran ve Holst, 2001) tarafından bulunan değerlerle de örtüşmektedir. ÖZET VE SONUÇLAR 2003 yılında fizibilite çalışmasının verdiği tavsiye doğrultusunda Peel Bölge İdaresinin çamurun yakılmasına devam edilmesi ve CWB sistemi yerine HWB sistemi kullanılması için vermiş olduğu kararın ne kadar doğru olduğu, işletme süresindeki tecrübeyle de doğrulanmıştır. HWB sisteminin güvenilir bir teknoloji olduğu ve eski CWB sisteminden çok daha verimli olduğu ispatlanmıştır. Zimpro prosesinin emekli edilmesinin de bu başarıda büyük payı vardır. Kokudaki azalma, hava kalitesindeki artış ve çamurun berterafındaki maliyet azalması bütün ilgili taraflara-atıksu arıtma tesisi, idareler, vergi ödeyen taraflar ve çevre halkı önemli avantajlar sağlamıştır. İlginizi çekebilir... Gemlik BUSKİ Ön Arıtma Tesisi'nde Koku Sorununa Aktif Karbon ÇözümüBursa'nın Gemlik ilçesinde, uzun yıllardır süregelen ve çevre halkını olumsuz etkileyen koku sorunu, BUSKİ Ön Arıtma Tesisi'nde kurulan aktif ... Nehir Suyundan İçme ve Kullanma Suyu EldesiNehir, dere, göl olarak tanımladığımız yüzey sularımız, organik madde, askıda katı madde ve ergimiş iyonlar ihtiva eden tatlı su kaynaklarımızdır.... İvedik İçme Suyu Arıtma Tesisi'nde Tercih SİSDOZ OlduSİSDOZ A.Ş., ASKİ İvedik İçme Suyu Arıtma Tesisleri 2. ve 3. kısımları için mevcut dozaj
pompalarının mekanik, elektrik ve otomasyonel modernizasyonu... |
||||
©2025 B2B Medya - Teknik Sektör Yayıncılığı A.Ş. | Sektörel Yayıncılar Derneği üyesidir. | Çerez Bilgisi ve Gizlilik Politikamız için lütfen tıklayınız.